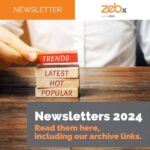
ZEBx Newsletters 2024
March 25, 2024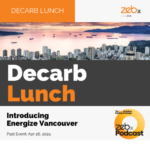
Apr 2024 Decarb Lunch Podcast: Introducing Energize Vancouver
April 29, 2024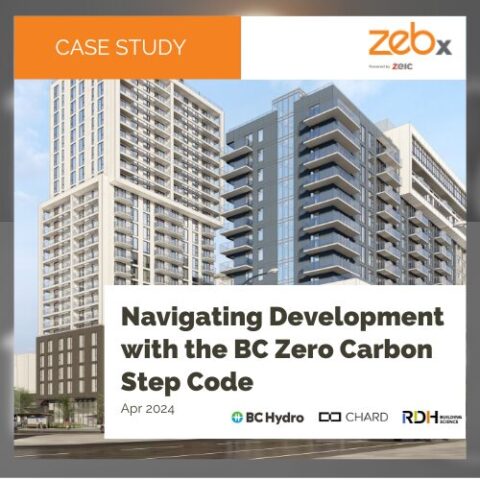
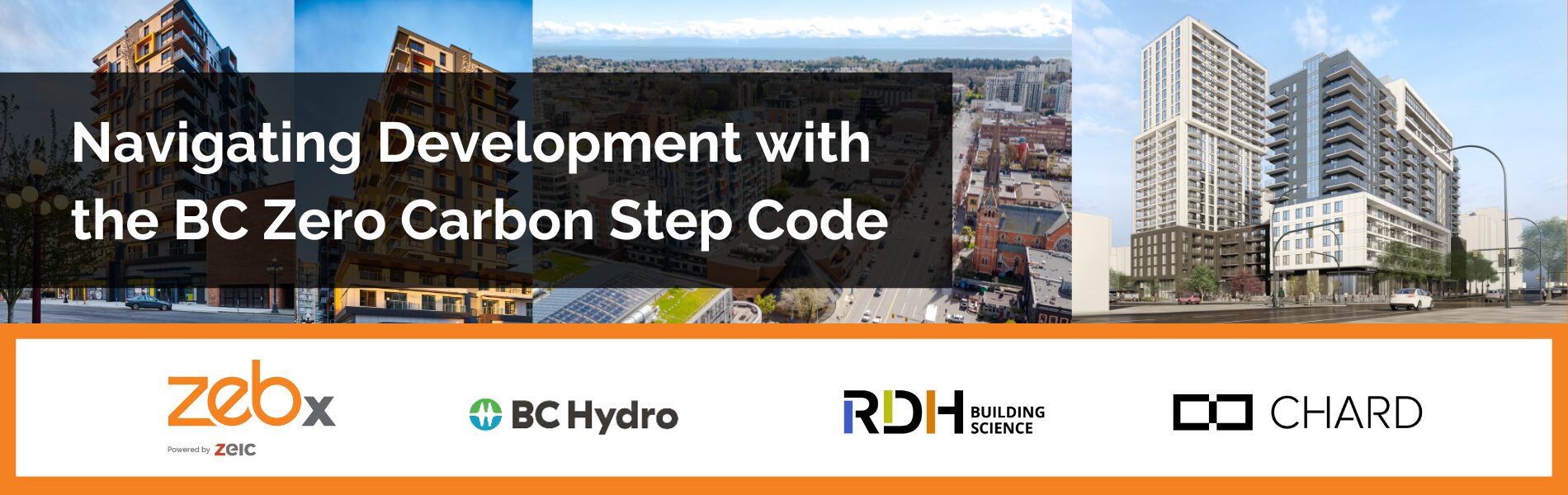
Guidance in Decision Making for Large-Scale Multi-Family Residential Developers
April 2024
Local governments are looking for developers to take a more proactive approach toward creating higher performance buildings. This document aims to support developers in this endeavour by providing a high-level cost index tool to assess the energy, emissions, and cost impacts of different building enclosures and mechanical design options early in the design process. It has been developed using a real case study project and focuses on large-scale multi-family residential buildings: rental apartments and condos.
This tool helps developers understand how different design choices affect their financial and building performance targets. It also aims to reduce the perceived financial uncertainty surrounding the top tiers of Energy and Zero Carbon Step Codes and help remove roadblocks in the development community to pursue higher performance projects. By using this tool and takeaways from the case study, developers can be better prepared for current and future regulations, reduce financial risks, forecast operating costs, and ultimately accelerate market transformation towards fully net-zero carbon construction.
The Next Step in Policy - Zero Carbon Step Code
The British Columbia Energy Step Code (ESC), enacted in 2017, introduced new energy metrics and approaches for accounting for energy use to the BC construction industry. As the Energy Step Code has been in force for several years1, achieving compliance is now relatively well understood by developers and the BC construction industry in general.
The Zero Carbon Step Code2 (ZCSC) is a new standard for building construction in BC. Its purpose is to reduce operational greenhouse gas (GHG) emissions from buildings. Like the Energy Step Code, which focuses on energy use and includes TEDI and TEUI targets, the Zero Carbon Step Code sets greenhouse gas intensity (GHGI) limits per square metre of floor area per year. The emission limit levels (EL for short) for large multi-family residential buildings are shown below. Municipalities across BC can now choose which Emissions Level of the provincial Zero Carbon Step Code to adopt into their local code.
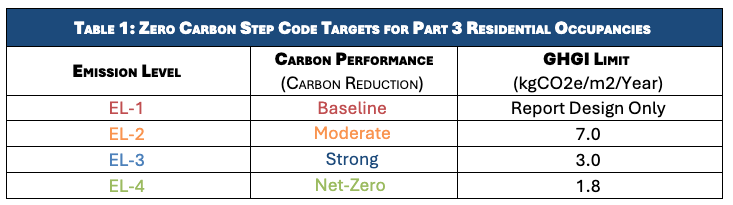
Table 1: Zero Carbon Step Code for Part 3 Residential Occupancies
Changes to codes in BC to address climate change are coming quickly: as of March 2024, 22 Authorities Having Jurisdiction (AHJs) have adopted the Zero Carbon Step Code, with some signalling their intent to require EL-4 (Net-Zero emissions) for all new Part 3 residential buildings starting in 2024. In addition to the Zero Carbon Step Code, another key code change affecting projects in preconstruction is the upcoming requirement to ensure that residential spaces can remain liveable during heat waves, which effectively steers designs toward including mechanical cooling in multi-family buildings.
Developers are recognizing the value of early-stage energy modelling – also referred to as parametric energy modelling – to optimize project cost and designs to meet the new regulations.
1 Note: As of May 1, 2023, the Energy Step Code has been fully adopted across BC, with the baseline now set at a minimum of the Step 2 level for energy efficiency. 2 See https://energystepcode.ca/requirements/ for more information.
What Does This Mean for Developers?
Many developer proformas are built around specific financial and project delivery models, intended to meet both code/permitting requirements and specific objectives of the developer, including monetary, marketability and branding goals. By understanding how code changes can impact typical building designs, developers can confidently proceed with projects and try to avoid costly late-stage redesigns.
In an effort to decarbonize the building industry, code and policy changes are shifting multi-family buildings from using natural gas to using electricity to power mechanical systems like heating, cooling, and domestic hot water. Furthermore, if carbon taxes on natural gas increase, this will affect future operational costs of gas-based systems. Sustainability (ESG) regulations, funding opportunities or investor requirements can also be tied to decarbonization requirements of buildings in BC. For these reasons, full electrification or mixed fuel approaches (combined gas and electric power) are becoming the normal for new multi-family buildings.
In addition to new codes and regulations, developers face constant fluctuations in the supply of materials and labour, changes in market demand for different asset classes, and lengthy rezoning and redevelopment timelines in some jurisdictions. High-level tools are essential to help developers pivot as needed to meet these ever-changing project demands. Developers need tools that consider:
- What combinations of mechanical and enclosure systems are suitable in BC?
- How will typical project capital costs be impacted?
- What are the changes in operational costs to consider for long term ownership?
- How to assess the financial impact of code and policy changes on projects that are already designed, to consider potential changes before breaking ground for construction?
Understanding the Impacts: A Case Study
To provide context and “ground-truthing”, a case study of an ongoing purpose-built multi-family rental development project in Victoria, BC was undertaken to analyze energy, emissions, and costing impacts of various mechanical and building enclosure design options. The subject project will provide close to 500 residential units, 4 commercial retail units, and approximately 8000 square feet of amenity spaces, and is comprised of two towers – 15- and 25-storeys – over a five-storey podium.
During the initial design stages, the project energy and carbon targets were not yet confirmed, and the project team wanted to understand the design and cost implications of potentially more stringent targets at the time of permitting. Table 2 shows the enclosure options that were considered, and Table 3 shows the mechanical system options. Twelve combinations of these enclosure and mechanical options were analyzed using the project’s energy model, to determine which combinations met the varying levels of the Energy and Zero Carbon Step Codes. Modeling results are summarized in Table 4.
For this case study, the building form and window to wall ratio were kept constant, having already been set before the schematic design and involvement of the energy modelling consultant, which is currently common practice.
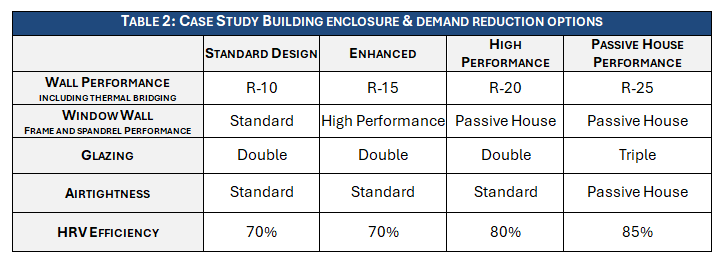
Table 2: Case Study Building Enclosure & Demand Reduction Options
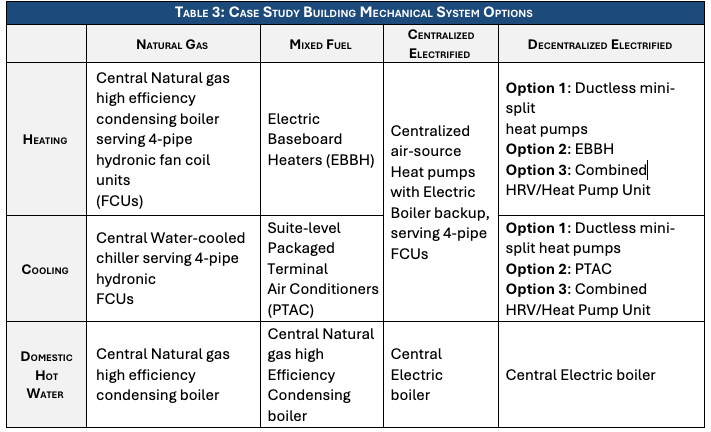
Table 3: Case Study Building Mechanical System Options
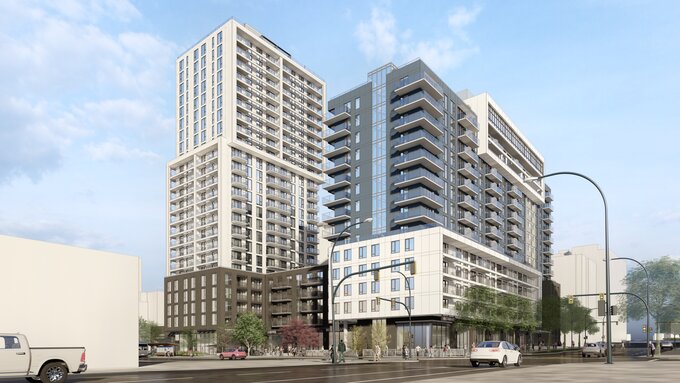
Renderings of multi-family rental development project in Victoria, BC
Energy, Emissions, and the Cost Index Tool
A cost index tool was developed from this study and is shown in Table 5. The costs of different design scenarios are indexed relative to a baseline design for the case study building. The baseline design meets Energy Code Step 2 with a natural gas heating and domestic hot water system and includes a centralized cooling system. This baseline design (although without cooling) has been the standard building design in recent years for many developers in BC. For this case study (and project), cooling was included in the baseline design – and all mechanical design scenarios – because future codes are trending towards requiring cooling to mitigate overheating related to climate change.
Tables 4 and 5 are intended to be used together. Table 4 shows what Energy Steps and Emissions Levels can generally be achieved with the combinations of building enclosure and mechanical system fuel types assessed. Table 5 then shows the cost implications of specific combinations of mechanical systems and enclosure designs.
As shown in Table 4, the baseline design required an Enhanced building enclosure to meet Step Code targets with natural gas-powered mechanical systems. This is because while the TEDI targets were met with standard enclosures, natural gas systems are not as efficient as electric and did not meet the TEUI targets.
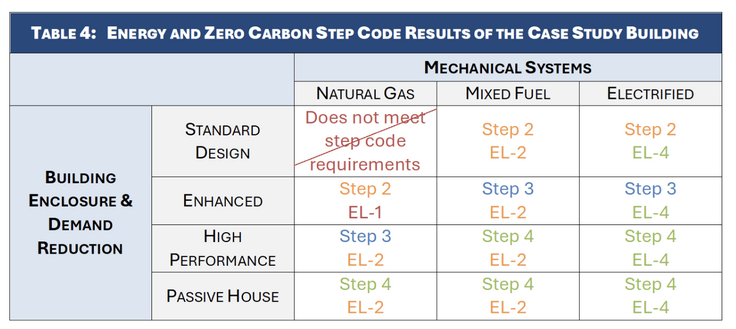
Table 4: Energy and Zero Carbon Step Code Results of the Case Study Building
Centralized natural gas and electrified systems, and decentralized mixed fuel systems were analyzed for all combinations of Energy and Carbon Step Code. Additional decentralized electrified approaches were considered in the analysis to assess the implications of achieving full building electrification in a variety of ways, though were only analyzed for Step 3 performance.
In Table 5, the left side of the matrix are the Energy Steps, and the top of the matrix are the different mechanical designs and fuel source(s) as outlined in Table 3.
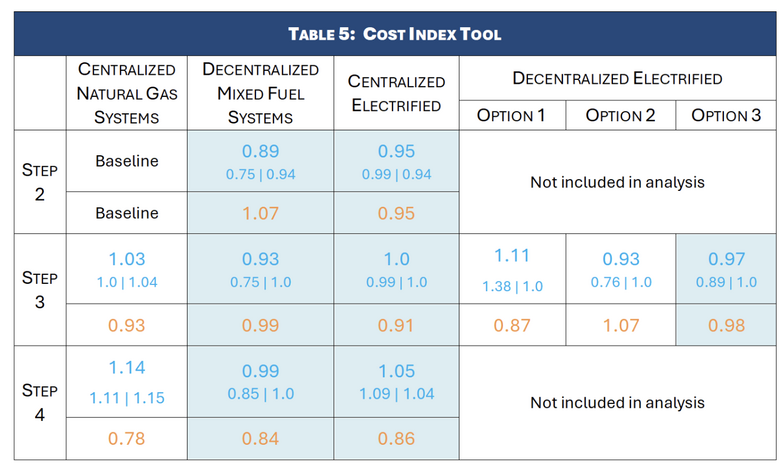
Table 4: Cost Index Tool
In the Cost Index Tool, the cost of the enclosure and mechanical systems for the baseline design is 1.0. The costs of different scenarios are presented as a factor of 1.0, relative to the baseline design cost. Each scenario is broken out into capital and operational costs over a 10-year period, and capital costs are further broken out into enclosure and mechanical systems. Renewals and maintenance are excluded, as most major renewals are beyond the 10-year milestone.
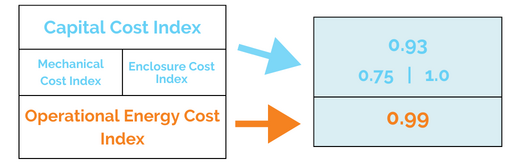
For each scenario box in Table 5, favourable results are shaded in blue, in which the 10-year net present value is lower cost than baseline design. Unfavourable results are not shaded, in which the net present value is costlier than baseline design.
Using the Cost Index Tool
The cost index tool is intended to be applied after the building form is generally established, for example after the window to wall ratio is set, and wall and roof areas are generally fixed, and an initial budget has been prepared for an initial design.
As an example, let’s say the initial budget for the baseline design capital costs are $30M for mechanical systems and $30M for the enclosure, and the 10-year aggregate operating costs are projected to be $5M. The blended 10-year cost for these systems and operations would be $65M.
Looking at Table 4, if the energy targets remained the same (Energy Step 2) but the building now had to meet EL-4 of the Zero Carbon Step Code, the mechanical systems would need to pivot from natural gas to fully electrified. Doing so would allow for the building enclosure to be downgraded from Enhanced to Standard Design To understand the cost impacts of these changes, go to Table 5.
In Table 5, to go from baseline design (natural gas) to a Centralized Electrified mechanical design meeting the same Energy Step 2, there would be an estimated net cost savings of $2.05M. This is in large part due to cost savings of the downgraded enclosure allowed by higher efficiencies of electrified mechanical versus gas systems.
>A breakdown of this calculation is as follows, remembering baseline design cost is 1.0:
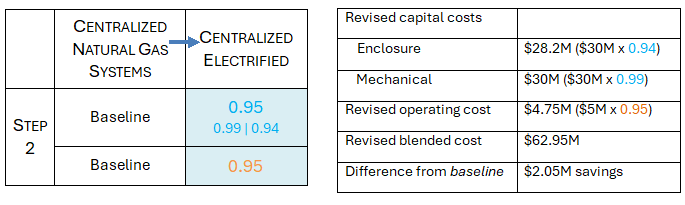
>It is important to note that the cost index tool is a ‘back of the napkin’ calculation to understand high-level implications of different system designs. The tool is not intended to be directly applied to project budgets and proformas without more specific design information. Deciding to redesign various systems may incur additional consulting fees and increase design and coordination time, which adds to project costs. Depending on the stage/level of design, consulting fees and added design time may outweigh cost savings of alternative approaches. There are diminishing returns at later stages in the design process.
>To optimize the building performance and costing further, consider using parametric energy modelling while designing the building form, to assess the cost, energy, and emissions impacts of different building enclosure variables like window-to-wall ratio, thermal performance of opaque wall and roof areas, and fenestration designs (windows); or mechanical variables like HRV efficiency and different types of mechanical systems. Focusing on these aspects of building designs to reduce overall heating and cooling energy demands is a further hedge against future uncertainty in operating costs due to fluctuations in utility rates – either gas or electric.
>Key Takeaways
>Results will vary for every project as costs and performance depend on the specific form and function of each building. While the insights are specific to the case study building and its unique design, many of the high-level lessons learned are applicable to large-scale multi-family buildings on a wider scale.
Case Study Specific Takeaways
- To use natural gas, the building design had to focus on reducing energy demand, i.e. using higher performance building enclosures than would be required with higher efficiency systems. The increased capital costs of higher performance demand-reduction designs were not offset by the operational and/or mechanical capital cost savings of gas systems.
- Like the natural gas systems, low-efficiency performance of electric baseboard heating in combination with separate cooling systems was close to exceeding TEUI targets at all Energy Step levels. Projects with designs using this mechanical approach may see the need to increase performance of the envelope to reduce energy demand to meet Energy Step Code TEUI targets, increasing initial capital costs.
- Heat pump technology for heating and cooling was the best approach as it allowed for flexibility of the enclosure design within TEDI/TEUI targets, such as optimizing/reducing wall or roof insulation, and increased thermal bridging tolerance at balcony and other interfaces.
- Projects using high-capital-cost mechanical systems are better off targeting Energy Step 4, to offset high capital costs with low annual operational costs. Step 2 projects using the same high-cost mechanical systems are unlikely to see low enough annual operational costs to justify the high capital costs.
- Projects using low-capital-cost mechanical systems (i.e. electric baseboard heaters) should also consider targeting Energy Step 4, to reduce operational energy costs associated with low-efficiency systems. The high operational energy costs of Energy Step 2 & 3 projects using low-efficiency, low-cost mechanical systems are likely to nullify the initial capital cost savings.
General Takeways for any New Multi-Family Project in BC
- Mixed fuel systems (electric + gas) may be a good choice for buildings constructed in the short-term that do not currently need to meet EL-3 or EL-4 of the Zero Carbon Step Code. However, operational or renewal costs may increase over the life of the building as policy, taxes, and utility rates change.
- Mixed fuel systems can be an appropriate solution for buildings with limited electrical capacity.
- Zero Carbon Step Code (EL-3) is extraneous. No mechanical options using natural gas could achieve this level or higher, but all the electric options comfortably achieved EL-4.
- For domestic hot water operational costs, gas is cheaper than electric for now due to current utility rate differences. However, carbon tax rate increases may change this and/or future codes may require the gas system to be replaced with electric at the next renewal cycle, which will increase cost and complexity to an otherwise typical renewal.
- Centralized vs. decentralized mechanical systems have no bearing on compliance with the Zero Carbon Step Code: if mechanical systems are all-electric, they achieve EL-4.
>Other Considerations
- >Although maintenance costs are not considered for this study, it is worth noting that centralized systems are typically easier and less expensive to maintain. Decentralized systems’ maintenance can be more difficult, intrusive, and time-consuming due to access considerations, which generally result in higher maintenance costs.
- Operating costs (mechanical systems) and interior comfort (mechanical and enclosure systems) affect the user experience and building management. Consider the end-user and building operator experience for each project.
- Some pieces of equipment for centralized all-electric systems have high initial costs when compared to natural gas centralized systems (centralized heat pumps versus natural gas boilers) due to current limited market availability of heat pump equipment. However, the cost of all-electric systems is anticipated to come down as market availability increases.
- The additional cost savings of centralized electric approaches when compared to natural gas systems are achieved by the elimination of an additional system required to provide cooling (i.e. inclusion of chiller + cooling tower in centralized natural gas systems).
>Assumptions
- >Capital costs were determined using real multi-family projects across BC and commercially available estimating software complete with up-to-date costing information. Enclosure costs are primarily windows and insulation, and do not include cladding, doors, roofing assemblies, balcony assemblies, or wall waterproofing membranes. Mechanical costs are for the systems described, including decentralized HRVs for each suite, but do not include plumbing, domestic hot water piping/fixtures, building automation & controls, or fire protection.
- > Energy modeling was done in accordance with typical Energy Step Code compliance requirements, which standardizes input assumptions like occupant behaviour, schedules, setpoints, etc.
- Operational energy costs were estimated using typical residential rates for electricity use within suites and commercial rates for energy used by centralized systems or in common areas. Electricity rates ranged from $0.0975 - $0.1078 / kWh. Natural gas rates ranged from $7.58 to $8.25 / GJ.
- Operational cost calculations included a 2030 carbon tax rate of $170/tonne of CO2e emissions, in line with the carbon tax projections outlined in the federal 2030 Emissions Reduction Plan.
- Operational costs provided in this analysis are only given in terms of energy costs, and do not take maintenance into consideration.
- All scenarios included a separate makeup air unit (MAU) to provide corridor ventilation/pressurization only. This approach remained unchanged for all scenarios. Mechanical systems for commercial retail units also remained unchanged.
- For natural gas systems, high performance condensing systems were used for applicable approaches.
- The case study building has a wall enclosure breakdown as follows: 37% windows, 24% spandrels, 39% typical walls.
A ZEBx publication written by RDH Building Science in collaboration with Chard Development Ltd.
Primary Authors: Maddy Kennedy-Parrott and Neil Norris
>Disclaimer: This is not an engineering report; however, engineering principles were applied to produce the results. Developers should discuss this report with their consultants for a broader understanding. Data and assumptions to support the findings are available upon request.
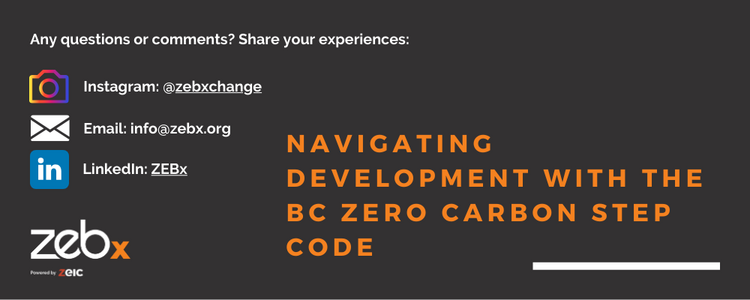